1、環模受力分析
如圖1所示,在環模與壓輥所組成的制粒系統
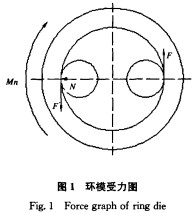

2、環模的有限元分析
2.1環模有限元模型的建立
考慮到所用計算機的配置及計算時間等因素,取環模的1/4作為研究對象,利用PROE軟件建立環模的1/4模型,然后將其倒入到Ansys軟件進行分析。
2.2單元形式的選取及網格劃分
由于環模多孔的特性,采用六面體單元時,在孔與孔之間的部分分網難度大,所以采用10節點的四面體單元(solid92)。
分網精度依據分析對象的受載,結構的尺寸和復雜程度來確定.環模的結構較為復雜,在高精度的情況下,對計算機內存的要求甚高,本研究取8級精度,采用智能(smart size)分網功能進行網格的劃分,劃分情況如圖2所示。
2.3施加載荷及邊界條件
在制粒的過程中,環模上所受的力除了作用在環模內壁上的壓力外,還有作用在模孔內壁上的摩擦力,在本研究的分析過程中,為了簡化分析難度,忽略了模孔內壁上的摩擦力,而通過前述的公式,運用能量守恒的原理,將摩擦力換算為環模內壁受到的壓力。
從環模的受力圖中可以看出,環模在直徑方向上受到對稱壓力的作用,當以顆粒機環模的受壓處為起點截取1/4環模后,在起點截面(現假設為豎直面)的兩邊,環模受到相同方向的壓力作用.而對于所截取的1/4環模的另一截面(即水平截面)來說,其左右兩邊的部分則受到方向相反的拉力作用.所以,為了能準確模擬環模的實際工況,在圖3所示的水平截面內施加反對稱邊界條件,在豎直的截面內施加對稱邊界條件。
環模所受的壓輥的壓力沿豎直方向施加。由于已將模孔內壁上的摩擦力換算為壓輥對環模的壓力,所以,只在豎直截面上孔與孔之間的部分施加載荷,然而,在環模內壁與豎直截面的交線上施加豎直向上的均布載荷比較困難,因此,為了簡化分析的過程,在豎直面截與環模壓帶部分相交所得邊線上的每個節點上,施加大小為275 N(11000/40,共40個節點)的集中載荷,如圖3所示。
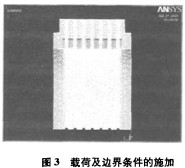
3、結果與分析
經過求解后,可以得到環模的變形圖和環模內部各點的應力等值線圖,如圖4、圖5所示.從圖4中的環模變形可以看出,環模不僅在水平截面上受到拉應力的作用,同時還承受彎曲應力的作用,完全符合環模實際工況和環模設計計算中的假設。
從環模內部各點的應力等值線圖中可以看出,環模內的應力分布比較均勻,在大部分區域內環模所受的應力小于21.2 MPa。
環模受到的最大應力為190 MPa,產生在集中力的加載處.而在實際的制粒過程中,力并不是以集中形式施加到環模上的,可以判斷,在正常的制粒過程中,環模所受的最大應力不大于190 MPa,小于材料的屈服強度345 MPa。
同時,從應力等值線圖中還可以看出.環模水平截面上的應力較大,最大應力在127 MPa到148MPa之間,這主要是由于環模在此面上同時受到拉應力和彎曲應力的共同作用,在制粒的過程中,隨環模的旋轉,環模的受力點也會在環模的內壁上沿周向移動,也就是說,在環模旋轉一周的過程中,環模的任意截面都會受到2次這種交變應力的作用。
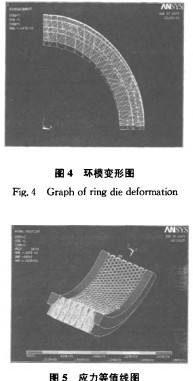
4、小結
從以上的分析中可以看出,環模受到的最大應力為190 MPa,小于材料的屈服極限,這就說明采用傳統設計方法設計的環模的結構強度滿足使用的要求.然而在實際制粒的過程中,環模內壁的磨損量比較大,環模的壁厚會不斷減薄,進而導致環模結構強度的減弱.所以,在環模的設計過程中,不僅要考慮結構強度,還要考慮環模所用材料的耐磨性.同時,環模在旋轉的過程中,其內部受到較大的交變應力的作用,當環模的壁厚減薄,結構強度減弱時,環模疲勞失效的幾率會有所增加。
三門峽富通新能源銷售顆粒機、顆粒機環模、飼料顆粒機、秸稈壓塊機等生物質燃料飼料成型機械設備。