硬度為HRC38-40,生產2500t飼料后表面有明顯的磨損,孔的內部開始出現凹痕。
目前國產x46Cr13合金鋼
顆粒機環模的使用壽命一般在5000-12000t左右,但生產特種水產飼料使用壽命偏低(由于孔徑和顆粒機型偏小),而大型設備則超過12000t。
①決定壓模使用性能和壽命的幾個因素
a.耐磨性:多數壓模的損壞是由于磨耗。壓模會因使用而引起表面磨損和模孔增大。壓模的耐磨性隨它的表面硬度、顯微結構和化學成分而變化。要使壓模得到最佳的耐磨性,關鍵在于材料的選擇和熱處理的方法。
b.耐腐蝕性:有些飼料成分和添加劑在高溫、高壓下會引起點蝕,從而腐蝕壓模材料。
因此,腐蝕是影響壓模性能的最關鍵的影響因素,必須加以控制。高鉻、高碳的壓模具有最好的耐腐蝕性。
c.韌性:在制粒過程中壓模承受很大的壓力,這種壓力能引起壓模的即時損壞:超過工作時間也會造成壓模的疲勞損傷。因此,壓模材料的選擇、熱處理的方法和模孔的多少都是決定壓模韌性的重要因素。
②環模材料的特性
a.耐磨性與韌性:提高壓模硬度(假定金屬結構固定不變)能增強耐磨性,但會降低壓模的韌性。換言之,用提高壓模硬度的方法來改進耐磨性,會增加脆性、降低韌性。因此必須將壓模的硬度限制在能保持使用所需最低限度的結構水平上。
b.耐腐蝕性與耐磨性和韌性:壓模的金屬結構差和耐腐蝕材料的化學成分不佳會降低耐磨性,壓模的沖擊韌性也比較差,較容易開裂。
c.韌性與孔數:如果使用一種質量較差的壓模材料而想通過增加孔數來提高制粒產量,是很難達到的。增加孔數很可能導致壓模的開裂。壓模材料(在熱處理的同時)具有不同強度和不同韌性的特點。有些材料的孔數要少一點才能保持最低程度的韌性和結構強度。
③壓模材料的選用
對于壓模的特性怎樣才算優質以及與選材之間的關系如何,很難下一個完整的定義。在市場上出售的各類壓模材料以及它們所具有的性能與缺點都要加以檢驗。目前用于生產壓模的材料一般可分為三大類:合金、鉻或淬硬的不銹鋼、滲碳不銹鋼。上述三大類材料有很多品種,它們的物理性質和化學性質又各不相同。每一類材料在制造過程中又都能通過特殊的熱處理方法改變其性質的。
a.合金壓模:美國多數飼料廠選用合金壓模。這種壓模由滲碳鋼制成,硬度很高,具有最佳程度的耐磨性和韌性。
壓模的滲碳硬化(表面硬化)是一種熱處理方法。即將壓模加熱至高溫,然后摻入足量的碳氣,這樣,鋼的外層吸收了很多碳。這種碳使鋼模的表面交得更硬,從而增加壓模表面的耐磨性。芯部材料中含碳較低,呈軟性,具有較高的沖擊韌性。這類壓模不易開裂。同時因為表面是碳化的硬層,因此芯部呈韌性,壓模更耐磨。但是這一類的壓模耐腐蝕性較差。
生產這類壓模所用的材料需根據成本和熱處理的工藝特性而定。一般來說,在選擇材料時要注意鎳的不同含量。因為含鎳量高,能增強韌性和增加壓模開孔數,但是材料成本也將提高。
b.鉻壓模有時也叫不銹鋼壓模。一般采用X40Cr13經淬硬或真空淬硬制成的壓模。
這種材料約含碳0.4%~0.5%,鉻12%~14%。此類壓模,能防止制粒原料的點蝕,但耐磨性和韌性比滲碳鋼壓模差。它們的外表面并不硬,但是芯部卻比滲碳鋼壓模硬。用顯微鏡觀察,標準的中性淬硬鉻壓模從表面到芯部晶相結構相當均勻。與滲碳鋼壓模的硬度呈逐步下降的情況不同,中性淬硬的鉻壓模從表面到芯部的硬度變化很小。
鉻的壓模具有很高的耐腐蝕性。在歐洲,由于飼料的腐蝕性非常大。所以壓模的鉻含量很高,而美國的飼料廠則不需要使用此類耐蝕程度的壓模。
c.滲碳不銹鋼壓模:此類壓模是一種更好的產品。滲碳不銹鋼壓模具有同合金壓模相似的淬硬表面,并且由于滲碳層有大量的碳化鉻,耐磨性一般很強,但是它們同滲碳合金一樣,從表面到芯部的硬度逐步遞減。
通過顯微鏡觀察,可以看到壓模外表聚集的碳化鉻呈現出許多的斑點。這些非常硬的粒子分散在整個滲碳層上,提高壓模的耐磨性。
由于此類壓模具有極好的耐磨性,能多次應用,因此噸顆粒飼料消耗壓模成本較低。此類壓模比合金壓模更耐腐蝕,但比鉻壓模要差一些。
(3)環模的轉速
設計環模轉速時要考慮四個問題:①制粒產量:它與轉速沒有正反比關系,存在最佳轉速范圍對應最佳產量;②顆粒成形率,太高轉速容易把壓制出來的顆粒甩碎,降低成形率,即等于產量下降;③不同飼料配方對應不同轉速,以壓制高品質飼料;④環模內徑尺寸,環模運轉過程中產生離心力,轉速太高,離心力就越大,影響顆粒機穩定性。綜合上面因素和結合世界制造顆粒機的經驗,環模的轉速應由環模內徑線速度確定。
根據經驗,模孔直徑小的環模,應采用較高的線速,而模孔直徑大的環模則應采用較低的線速。環模的線速,會影響制粒效率、能耗及顆粒的堅實度。在一定范圍內,環模的線速提高,產量增大、能耗提高,顆粒的硬度和粉化率指數上升。一般認為,模孔直徑為①3. 2—6. 4mm時,壓模的最高線速可達到10. 2m/s;模孔直徑為中16~19mm時,壓模的最高線速應限制在6.1~6. 6m/s。而在實際應用中,國內外廠商選用的環模線速均在3. 5~8. 5m/s。而一機多用的情況下僅使用一種線速度,是不能適應不同種類飼料加工的要求的。比較普遍的現象是,大型顆粒機生產小孔徑顆粒飼料時質量不如小型顆粒機效果好,尤其是在生產直徑3mm以下的畜禽飼料和水產飼料時特別明顯。文獻[8]認為是環模的線速過低和壓輥直徑過大是主要因素,這些因素會造成壓制物料穿孔速度過快,從而影響硬度和粉化率指數。最理想的解決辦法是采用無級調速。由于位置和投資成本的限制,也不太現實。CPM等多家公司采用可調雙速傳動,以適應不同孔徑和原料的加工需要,獲取最佳的生產效果,提高顆粒機的通用性。國外還有多家公司采用同一種機型配置2-3種不同的環模線速,供客戶選擇,以適應不同的專業生產要求。因此最佳環模線速的選擇是一項具有現實意義的研究課題。本課題將在第四章進行環模轉速對生產率影響的試驗研究。
2.4.2壓輥結構
壓輥主要由壓輥偏心軸、壓輥殼、滾動軸承等組成。壓輥的作用壓輥的作用是將物料擠壓入模孔,在模孔中受壓成型。
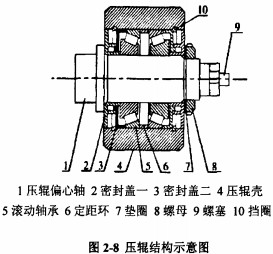
(1)壓輥的材料及表面
模、輥線速度基本相等,而輥的直徑小,故壓輥磨損率比壓模大。若輥模同時更換,則壓輥硬度應高于壓模5-6HRC。故壓輥一般用高碳合金鋼制造。為使物料壓入模孔,壓輥與物料間必須有一定的摩擦力。壓輥做成不同形式的粗糙表面,以防止壓輥打滑。
①拉絲輥面:是目前最常見的一種,防滑能力較強,但物料有可能向一邊滑移。如將拉絲槽做成兩端封閉型,則可以減少這種滑移。
②帶凹穴的輥面:凹穴內填滿物料,形成摩擦表面摩擦系數較小,物料不易側向滑移。
③槽溝輥面:在輥面上有窄形的槽溝以增加摩擦力,與凹穴輥面一樣,物料不易側向滑移。
④碳化鎢輥面:輥面嵌有碳化鎢顆粒,表面粗糙,質硬耐磨。對于磨損壓輥嚴重及粘性大的物料,這種輥面尤為見效。具有碳化鎢涂面的壓輥,使用壽命比拉絲輥長3倍以上。但在使用時,務必使該輥定位準確,避免磨損壓模。
每一壓輥繞其中軸旋轉。中軸為偏心軸,旋轉調節螺栓使偏心軸轉動,壓輥的旋轉中心軸也隨之改變,由此可改變壓輥與壓模的間隙,以使不同原料或產品獲得理想的壓制效果。
(2)壓輥的技術參數
壓輥的數量:環模顆粒壓制機的壓輥一般為2~3只,特殊情況有多只;根據受力分布合理性,以3只壓輥為最佳。平模顆粒壓制機一般為2~5只,常用4只。壓輥直徑:對于二輥式顆粒壓制機的輥模徑比為0. 43~0. 55,三輥式為0.39~0. 46。平模顆粒壓制機壓輥的直徑應是環模的1.6倍,才能使兩者壓實層相同。在實際應用中,在兩種機型功率相同的情況下,壓輥直徑比為1. 25~1. 77。
壓輥的表面硬度與使用壽命:壓輥的材料表面硬度在理論上應低于壓模的表面硬度HRC2-3,這樣能保證環模的低磨損和使用壽命。原則上新模配新輥,模輥的最佳壽命比為1:1,國外常用1:2,國內使用1:3。
(3)模輥間隙
模輥間隙調整極為重要,間隙過小,會加劇磨損;間隙過大,會造成打滑,影響顆粒質量。模輥間隙一般為0.1-0.4,對環模型顆粒機一般物料間隙為0.1-0.3,壓草粉為0.5。對平模顆粒機一般間隙為0.005-0.3。
壓輥安裝到環模內后,利用壓輥偏心軸,可以調整壓輥外表面與環模內表面之間的間隙,壓輥應調整到與環模輕微接觸且剛好能帶動壓輥似轉非轉為宜。壓輥調節原理如圖2.26所示。松開壓輥調節螺栓3,通過擰動抵在偏心調節凸緣上的與壓輥調節螺栓3對應的調節螺栓就可調整壓輥與環模之間的間隙。調至正確位置后,擰緊旋松的調節螺栓并鎖緊。
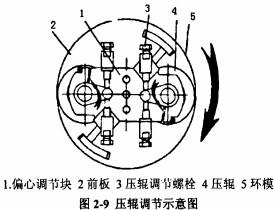
輥模間隙自動調整裝置的種類很多,基本原理是采用氣動或液壓執行機構,自動調節。氣動輥模間隙調整裝置的工作原理:利用氣源的壓力差帶動氣動馬達旋轉,氣動電機通過花鍵帶動蝸輪蝸桿機構轉動,蝸輪通過梯形螺旋前后往復運動,而調節桿兩端安裝在球面軸上,這樣調節桿可在一定范圍內擺動,帶動調隙輪轉動,從而買現調節模輥的間隙。此外,在環模堵料時,能使壓輥迅速遠離環模內表面,這樣便于清理,節省時間,提高效率。
三門峽富通新能源銷售顆粒機、
秸稈壓塊機、飼料顆粒機、
木屑顆粒機等生物質燃料飼料成型機械設備,同時還有大量的生物質顆粒燃料出售。