Barmac9000型破碎機是三峽工程項目從新西蘭購買的一種制砂效率很高的新型破碎機。由于破碎料源花崗巖質地堅硬,機內耐磨件消耗極快,尤其是轉子拋料頭,工作約100 h就需更換一次。為使耐磨件國產化,解決進口配件價格昂貴,到貨周期長且難以滿足工程連續高強度生產的需要等問題,我們對該機內耐磨件進行了反復的試制,取得了較好的使用效果。
1、Barmac9000型破碎機耐磨件的磨損機理
Barmac9000型破碎機的最大進料尺寸為57 mm,轉子轉速為1 000~1 800 r/min,制砂母巖是斑狀花崗巖,SiO2占72. 21%,其干抗壓強度為138.8~17 5.1MPa。工作時膠帶機將被碎物料從設備項部給入,一部分物料通過控制器進入高速旋轉的轉子,轉子將物料加速后以58~60 m/s的速度拋射入破碎腔中;另一部分物料瀑布式定量地溢入破碎腔,轉子射出的物料與溢入破碎腔物料相互劇烈沖擊,碰撞瞬間物料爆裂,經反復碰撞后,物料從57 mm破碎成4~5 mm的細散顆粒。由此可見,由這些易損件(導料板上、下耐磨板、轉子拋料頭、分料盤、給料孔套等)組成的轉子是破碎機的心臟。而其中的給料孔套不僅要承受由上部高速射落下的高硬物料強烈沖擊,而且還要將物料以較高的線速度和高的動能射向腔內。這些易損件處于磨粒磨損和沖刷磨損的復合磨損狀態,工況條件相當惡劣,故要求其材質具有高硬度的同時還必須有足夠的沖擊韌性。
2、耐磨件材質的選用
根據主要耐磨件的磨損機理,我們選用多元高鉻合金耐磨鑄鐵進行試制,并通過爐前孕育處理。1以提高綜合力學性能。在成分控制上主要考慮要利于控制初生碳化物和共晶碳化物的數量,利于改善碳化物的形態與分布,利于堅硬碳化物能十分牢固地鑲嵌在基體上。為此我們在已有研究的基礎上,進行了試驗。發現確定成分的關鍵是要嚴格控制碳和鉻的含量及Cr/C比。適當含量的碳和鉻,可獲得適當量的M7C3。型碳化物;合適的Cr/C比,可基本控制奧氏體的穩定性和可硬性,從而獲得理想的基體組織。本試驗合金的化學成分控制見表1。
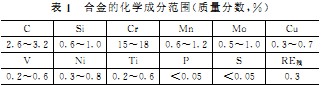
3、鑄件生產工藝
試驗原材料用GCr15及少銹碳素廢鋼、金屬鉻、鉬鐵、釩鐵、鈦鐵,用低S、P生鐵。中頻感應電爐熔煉。經實驗,各元素的燒損率為:C、Cr、Mo、W、Ni≤5%,V≤10%,Mn為5%~20%。為保證加入的多種合金能完全溶解,出爐溫度控制在1500~1550 ℃,并用釩鐵、鈦鐵和稀土硅鐵進行爐前孕育處理,澆注溫度1380~1 400℃。
采取濕型鑄造,由于鑄鐵中合金含量高,流動性差,收縮量大,導熱性差,因此在設計鑄件工藝時,采取順序凝固原則,力求消除收縮缺陷,提高致密度;同時,為了保證鑄件組織致密,要加強擋渣,防止渣粒及未熔合金成為裂紋源存在于鑄件中。
4、熱處理工藝
在確定淬火溫度前,我們對試樣的硬度、沖擊韌度與淬火溫度的關系進行了測定(見圖1、2)。可見,隨著淬火溫度的升高,沖擊韌度緩慢降低,而硬度曲線呈現峰值,峰值附近為最佳淬火溫度范圍,即850~920℃:,綜合考慮后,確定淬火溫度為870~890℃,保溫時間為2. 5~4.0 h,空冷。具體淬火溫度及保溫時間應根據鑄件的壁厚進行適當調整,對于形狀復雜的厚壁件,還必須考慮淬火加熱速度,應避免因相變或高的加熱溫度梯度而引起高的應力,加熱速度一般不高于30℃/h。一旦鑄件加熱至暗紅色,也就是通過塑性變形溫度而使應力降低得足夠多時,才可加速加熱。
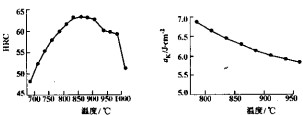
合金淬火后,必須進行低溫回火處理以消除內應力,改善其韌性。回火溫度控制在(200~250)℃,保溫6h。
5、組織、性能及使用考核
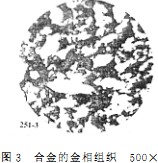
采用(德)蔡司臥式顯微鏡對經熱處理后的多元合金鑄件進行觀察,其組織為馬氏體基體十菊花、團塊狀碳化物,其中碳化物含量約占45%(見圖3)。為尋找特定工況下材料韌度與硬度的最佳配合,對多元合金鑄鐵經熱處理后的力學性能按照GB8263-87的標準進行檢測,結果是:硬度64~67 HRC;沖擊韌性
5. 5~6.5 J/cm
2。
對Barmac9000型破碎機中的轉子拋料頭、分料盤、給料孔套等主要耐磨件進行裝機生產考核,使用壽命為120~130 h,而進口原件約為100h,其它耐磨件的使用壽命與進口件相當。這樣,使用多元高Cr合金鑄鐵生產的配件,破碎機的生產成本大大降低,同時也滿足了工程連續高強度生產的需要,到目前,利用該材料己生產出配件10余噸,為國家節省了大量外匯。同時也為引進該機器,提高破碎效率,降低制砂成本,設備配件國產化提供了可靠的技術支持。