超細粉碎和超細顆粒的制備技術是制取超細粉體材料的主要技術手段。應用在粉體加工領域的微粉碎設備系統的主要粉碎機理和結構特點有以下幾種形式:輥磨類微粉碎系統;反擊式、錘式微粉碎機系統;球磨類微粉碎系統。目前,向超細粉碎設備提供原料的加工設備以輥磨設備居多,主要有懸輥式盤磨機(雷蒙磨)、輥式磨(立式磨)、輥壓磨和各種輥磨的變異設備等。由于雷蒙磨本身的一些結構特性和使用特點以及比較可靠的運轉率,適用于重晶石、方解石、鉀長石、滑石、大理石、石灰石、陶瓷、玻璃等莫氏硬度不大于7級,濕度在6%以下的多種物料的制粉加工,成品粒度在100目- 425目范圍內任意調節。目前雷蒙磨已在國內外的礦業、化工、建材和冶金等非金屬礦產品加工上得到了廣泛應用。
雷蒙磨制粉的原理如下:物料經粉碎到所需粒度后,由提升機將物料送至儲料斗,再經振動給料機將料均勻連續的送人雷蒙磨主機磨室內,由于旋轉時離心力作用,磨輥向外擺動,緊壓于磨環,鏟刀鏟起物料送到磨輥與磨環之間,因磨輥的滾動而達到粉碎目的。物料研磨后的細粉隨鼓風機的循環風被帶入分析機進行分選,細度過粗的物料落回重磨,合格細粉則隨氣流進入成品旋風集粉器,經出粉管排出,即為成品。在雷蒙磨磨室內因被磨物料中有一定的水分,研磨時生熱,水氣蒸發,以及整機各管道接口不嚴密,外界氣體被吸入,使循環氣壓增高,保證磨機在負壓狀態下工作,所增加的氣流量通過余風管排入除塵器,被凈化后排人大氣。磨輥和磨環是雷蒙磨設備上的主要消耗備件,我廠長期以來使用高錳鋼制造,存在使用壽命短、備件更換頻繁、備件消耗量大,以及制粉成本高等不足。高錳鋼是一種強韌性良好,并有優良形變硬化能力的鋼種,在三向擠壓狀態下高錳鋼的加工硬化非常明顯,表面硬度可達910 Hv。但用于雷蒙磨磨輥、磨環,因沖擊不足,加工硬化效果差,400 Hv以上的硬化層深度不足0.3 mm,距表面1.8 mm處的硬度為255Hv,接近高錳鋼磨輥、磨環的原始硬度240 Hvo因此,高錳鋼用于制造雷蒙磨磨輥、磨環是不合適的。研究成本低廉、工藝簡便、性能優良的雷蒙磨磨輥、磨環材料具有極其重要的意義。
1、高硼耐磨鑄鋼基礎研究
1.1 高硼耐磨鑄鋼特點
硼元素在地殼中的含量約占3×10 -4%,接近鎢、鉬的含量,是我國富有的元素,價格低而且穩定。隨著鉻、鉬、鎳、鎢、釩等合金元素在鋼鐵材料中使用量的不斷增加,價格飛速上漲,供應日趨緊張,導致普通鋼鐵耐磨合金生產成本不斷攀升。硼在- Fe中的溶解度小于0.000 4%,在7- Fe中的最大溶解度也只有0.02%[3],加入鐵中的硼大部分將會形成硼化物。碳在鐵中的固溶度比硼高得多,在a-Fe中僅為0.021 8%,而在1- Fe中高達2.11%,因此,通過調節鑄鋼中硼含量和碳含量可以實現對硼化物體枳百分數及基體含碳量的控制,使高硼鑄鋼具有優異的耐磨性和強韌性。
目前,在鋼鐵耐磨材料中,已經發現的耐磨硬質相主要有碳化物和硼化物兩大類。以碳化物為耐磨硬質相的鋼鐵耐磨材料研究較多,而以硼化物為耐磨硬質相的鋼鐵耐磨材料研究較少,究其原因是以往的研究結果表明,在鋼鐵材料中如果硼含量超過0. 01%,將會在晶界上形成脆性硼化物,使材料韌性顯著降低H.列。大量研究發現,硼是應用非常廣泛的一種元素,加入合金鋼中,硼能顯著提高鋼的淬透性。微量硼對耐熱鋼有提高高溫強度和蠕變性能的作用,加入不銹鋼和耐熱鋼中可以改善熱加工性能。在白口鑄鐵中加入微量硼還可以細化共晶碳化物,改善碳化物的形態和分布,提高白口鑄鐵力學性能。從降低成本和提高耐磨性的角度出發,對高鉻鑄鐵進行加硼的試驗研究發現,添加適量的硼和采取合適的熱處理工藝,可以使高鉻鑄鐵的碳化物細化,基體淬透性增加,并使高鉻鑄鐵的硬度和韌性同時得到提高,從而增加了材料的耐磨性。在工程應用中已經證實,硼加入結構鋼中可以代替和節省一部分稀貴元素,如鎳、鉻、錳、鉬等合金元素,在汽車工業中用硼鋼代替40Cr鋼,其使用壽命不低于鉻鋼。另外,利用硼具有優越的屏蔽熱中子和抑制俘獲射線的核特性,而且鐵本身又是輻射屏蔽中常用的材料,因此,研究既有優良核特性又有足夠結構強度的高硼鋼,始終是人們追求的目標。高硼鋼中的硼含量從0. 12%到4.0%,采用真空熔煉、電磁攪拌等先進工藝,準確控制成分,穩定硼的回收率,使硼均勻分布于鋼中,可以穩定鋼的性能。
受上述研究工作啟發,我們開發的高硼鑄鋼主要以高韌性的馬氏體為基體,在基體上分布有硬度高、熱穩定性好的硼化物,可以確保高硼鑄鋼具有優異強韌性的前提下,還具有高的硬度和優良的耐磨性,可以克服目前廣泛應用的以碳化物為主要耐磨硬質相的鐵基耐磨合金(如高鉻鑄鐵、鎳硬鑄鐵等)脆性大,使用中易斷裂和剝落的不足,也可以克服無耐磨硬質相的鐵基合金(如高錳鋼、低碳合金鋼)硬度低、淬透性與耐磨性差的不足,在雷蒙磨磨輥、磨。環上發揮其優異的耐磨性能,延長其使用壽命。
1.2高硼耐磨鑄鋼的成分
高硼耐磨鑄鋼成分見表1。其中碳含量控制在0.4%以下,主要是為了在淬火處理后獲得強度高、韌性好的板條馬氏體基體。碳含量過高,淬火組織組織中易出現脆性大的高碳馬氏體,降低高硼鑄鋼的強韌性。硼是高硼鑄鋼中的主要合金元素,加入硼主要是為了獲得一定數量的高硬度硼化物,改善鑄鋼耐磨性。部分硼溶予基體,可以改善基體的淬透性和淬硬性,最終可改善高硼鑄鋼的耐磨性。另外還加入適量的鉻和錳主要是為了強化基體,改善高硼鑄鋼淬透性。
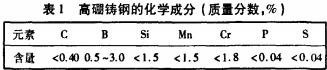
1.3 高硼耐磨鑄鋼顯微組織和力學性能
高硼鑄鋼的鑄態組織見圖1,由初生奧氏體和共晶組織組成。在普通低碳鋼中如果不加硼或者硼微量加入,其鑄態織將由大量鐵素體和少量珠光體組成。盡管高硼鑄鋼的碳含量在中、低碳鋼范圍內,在普通鑄造條件下卻獲得了大量的共晶組織。由Fe -B合金二元相圖可知,高硼鑄鋼的凝固過程不同于普通低碳鋼,由于高硼鑄鋼中硼含量高,其凝固過程是首先析出初晶',由于Cr、Mn、B等元素在r相的分配系數小于I,因此隨后^r -邊向液相中排出Cr、Mn、B等元素,一邊長大。當B含量接近3.8%左右時,在和r初晶相接的富集Cr、Mn、B的殘留液相中發生_y+硼化物的共晶反應。X射線衍射分析表明,高硼鑄鋼的共晶硼化物是Fe2(B,C)。基體組織是鐵素體和珠光體,它們是由初生奧氏體和共晶奧氏體在凝固冷卻過程中轉變而成。高硼鑄鋼中的Fez(B,C)具有高硬度和良好的熱穩定性,測試其顯微硬度達到l 400 Hv~1 520 Hv。另外,Fe2(B,C)硼化物沿晶界呈網狀分布。
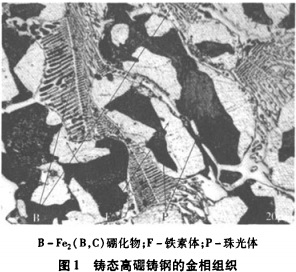
淬火溫度對高硼鑄鋼顯微組織的影響見圖2。淬火溫度低于950℃時,高硼鑄鋼高溫奧氏體中溶解的硼、鉻等元素少以及碳、錳、鉻等元素在奧氏體中分布的均勻性較差,奧氏體的整體淬透性低,淬火組織中存在部分珠光體和少量鐵索體,見圖2a,珠光體和鐵素體的存在,導致高硼鑄鋼硬度較低,見圖3。隨著淬火溫度升高,高溫奧氏體中溶解的硼、鉻、錳量增加,同時碳、錳、鉻等元素在奧氏體中分布的均勻性也增加,奧氏體淬透性不斷提高,淬火組織中鐵素體消失,珠光體減少,見圖2b,且硬度提高。淬火溫度1 000℃時,珠光體已完全消失,淬火組織已完全轉變成了高硬度的馬氏體組織,見圖2c、2d。圖4的X射線衍射分析表明,硼化物穩定性好,高溫下不分解,仍為Fe2(B,C)。另外,隨著淬火溫度的升高,硼化物由連續網狀向孤立狀分布轉變,有利于高硼鑄鋼韌性的提高,見圖3。
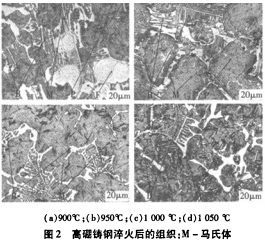
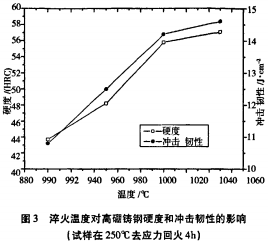
2、高硼鑄鋼雷蒙磨磨輥磨環的制造和應用
2.1 高硼鑄鋼雷蒙磨磨輥磨環的制造
高硼鑄鋼雷蒙磨磨輥磨環采用中頻感應電爐熔煉,爐料為生鐵、廢鋼、硼鐵(含19 %B)、硅鐵(含75%Si)、錳鐵(含78%Mn)和鉻鐵(含62%Cr)。待鋼水過熱至1 600℃~1650℃時,經造渣、扒渣、硅鈣合金預脫氧和鋁終脫氧后,加入硼鐵合金。澆包內加入0.2%稀土硅鐵。采用水玻璃石英砂造型,表面烘干,依照理論和實踐數據,確定鑄件收縮率1.85%。鋼水澆注溫度l 450℃~1 500℃,澆注時先小流,中間要快,后期慢澆使鑄件充分補縮,并點冒口1~2次。磨輥、磨環采用臺車電爐加熱,水玻璃溶液冷卻,加熱溫度1 020℃~1 050℃,保溫4h。在井式爐內回火6h~8 h,回火溫度控制在230℃~280℃。
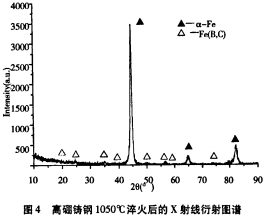
2.2 高硼鑄鋼雷蒙磨磨輥磨環的檢測及工業應用
采用MITECH - H1200型便攜式硬度在高硼鑄鋼雷蒙磨磨輥、磨環上測試了硬度,硬度值大于55HRC,硬度均勻性好,硬度差小于2 HRC。在此基礎上,對磨輥、磨環進行了磁粉探傷,未發現裂紋和尺寸大于1.5 mm的夾雜物。高硼鑄鋼雷蒙磨磨輥、磨環已在我廠的四輥雷蒙磨粉機上進行了工業試驗,用于將粒度20mm左右的膨潤土和泡砂石,研磨成300目一350目的細粉。結果發現,高硼鑄鋼雷蒙磨磨輥、磨環使用安全、可靠,使用中無剝落、開裂現象出現,由于其硬度高,耐磨性好,使用壽命比高錳鋼磨輥、磨環提高120%—160%。另外,高硼鑄鋼中硼是主要合金元素,硼鐵價格僅為16 500元/t,且不含價格昂貴的鉬、鎳等合金元素,因此高硼鑄鋼雷蒙磨磨輥、磨環成本低,推廣使用具有良好的經濟和社會效益。
3、結論
1)B含量為0.5%~3.O%和C含量<0.4%的高硼鑄鋼的凝固組織由硬度高達1400 Hv一1520 Hv的Fe2(B,C)、珠光體和鐵索體組成,且硼化物沿晶界呈網狀分布。
2)高硼鑄鋼在高溫加熱過程中出現了硼化物溶解現象,而且加熱溫度越高,硼化物溶解越明顯。隨著硼化物的溶解,硼化物形態也發生了明顯變化,由連續網狀向斷網狀和孤立狀轉變,隨著加熱溫度升高,硬度明顯提高,且韌性也略有提高。
3)高硼鑄鋼用于制造雷蒙磨磨輥、磨環,工藝簡便、成本低廉,硬度分布均勻,用于研磨膨潤土和泡砂石,使用壽命比高錳鋼磨輥、磨環提高120%~160%。