0、引言
水泥熟料
破碎機錘頭既受高沖擊力的鑿削磨損,又受高應力的犁削、沖刷磨損,因此錘頭材質需要有足夠的韌性和硬度才能耐磨。在立窯下使用的熟料破碎機,由于熟料溫度一般為200~300℃,時常高達500℃,要求錘頭還應具有高的抗回火性能。因此,錘頭材質既要求高硬度,又要有足夠韌性,還要耐300℃左右高溫。近年來,人們一直研究一種既耐磨又使用可靠的熟料破碎機錘頭,如高錳鋼合金化、超高錳鋼、各種成分的合金鋼等,但壽命提高倍率都不高。有的采用復合錘頭,由于工藝復雜,技術不過關,時常發生脫落,或錘柄過早磨損,達不到預期效果,因此也沒有推廣應用。
針對熟料破碎機錘頭材質存在的問題,我們經過兩年多的試驗,研制出一種高韌性、高硬度,并可承受500℃以下高溫的用于熟料破碎機的耐磨錘頭。錘頭重量1.8~58kg/只;配套破碎機產量10~ 200t/h;錘頭硬度HRC62~65,沖擊韌性8~12J/CIT12;一副錘頭根據不同工況條件可破碎熟料8 000~150000t,噸熟料純磨耗為1.0~3.0g。
1、幾種錘頭耐磨材料的分析
1.1 高錳鋼及改性合金化高錳鋼錘頭
目前水泥廠礦山常需碎碎800~1500mm大塊物料,如石灰石、頁巖等,故仍采用高錳鋼錘頭。但由于它的屈服強度低,使用中易產生塑性流變,因此,一些國家多在高錳鋼中加入2%以上的Cr. Mo. Ni等合金元素,以提高其屈服強度和硬度,為在厚大斷面上也能生成全奧氏體,又研制出含錳量16%~18%的超高錳鋼,國內近年來也有生產,并取得較好的效果。但采用高錳鋼或超高錳鋼錘頭破碎水泥熟料時,使用壽命不長。
1.2 合金鋼錘頭
中、小型破碎機錘頭由于受沖擊力不很大,高錳鋼不能充分發揮其沖擊硬化作用,所以國內外近年來研制了多種合金鋼材質的錘頭,硬度一般可達HRC45~ 55,使用壽命比高錳鋼提高0.5~1倍。但總體來看還不能使用戶滿意,特別是破碎熟料,在國內只能使用7d左右。
1.3 高鉻鑄鐵復合材料錘頭
國內小型破碎機5kg以下錘頭,近年來開始采用高鉻鑄鐵。高鉻鑄鐵的耐磨性可達到高錳鋼的4倍。
國內對10~20kg錘頭,采用半機械半冶金的復合錘頭,錘柄為中低碳鋼,錘頭用高鉻鑄鐵,包裹澆注,使用中常有錘柄先磨穿或錘頭掉塊等現象,使用不穩定,加上工藝比較復雜,推廣受制約。
進口復合錘頭,原來使用較好的有冀東水泥廠破碎石灰石的90kg錘頭,為雙金屬熔合澆注,錘柄為合金鋼,錘頭為高鉻鑄鐵,但使用一段時間后,也發生了錘柄磨損嚴重、錘頭易剝落掉塊的現象。后來國外改為超高錳錘頭,即含錳量18%左右的整體鑄造錘頭。
美國ESCO公司研制出一種組合式錘頭,如圖1所示。該錘頭的特點為用銷軸固定高鉻錘頭部分,錘柄為低合金鋼,實際效果如何未見進一步報道。
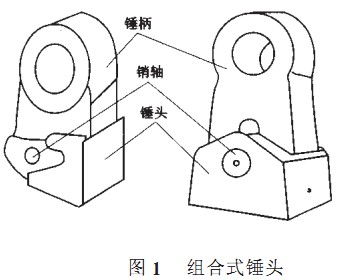
2 熟料破碎機高韌性耐磨錘頭的研制
2.1 化學成分的設計
熟料破碎機錘頭按磨損理論,硬度應為熟料硬度0.8~1.3倍,熟料硬度一般為HV500~550,錘頭硬度應達到HV600~650,相當于HRC64以上,同時還要在200~300℃條件下長期使用,因此要具有抗回火性能。
為達到這些性能,我們把金相組織定為回火馬氏體基體,加上30%左右的Cr7C3型高硬度碳化物,并且碳化物應該是斷網的、塊狀的,使之既有高硬度、耐磨,又有高韌性,還能耐一定高溫。按此思路進行成分設計。
1)碳(C)和鉻(Cr)含量
圖2為Fe - Cr -C系的室溫切面(2 3,從圖中可見①高碳、低鉻時,容易出現M3C型碳化物;②低碳高鉻時易出現M4C型碳化物;③鉻與碳配合恰當時才可得到M7C3型碳化物。從圖可知當碳(C)在2.6%~3. 0%,Cr在22%~25%時,可得到Cr7C3碳化物,硬度為HV1700,可大大提高金屬的耐磨性。但碳量太高超過共晶碳量會發生粗大的初生碳化物,質很脆,在磨料沖擊下會碎裂,并且碳量增加,韌性降低。所以碳量設計范圍為2. 4%~3.2%。
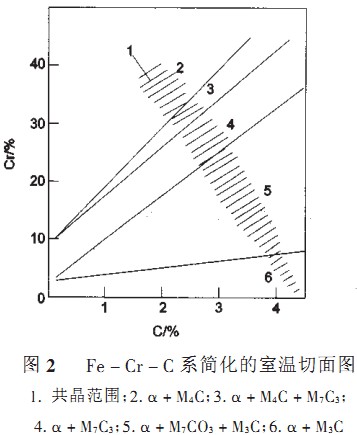
鉻一部分形成Cr7C3型碳化物及二次碳化物,另一部分提高機體的淬透性.使它既有足夠韌性,又有高的硬度,故鉻含量控制在18%~24%。
2)鉬( Mo)含量
鉬一部分進入碳化物,一部分溶入奧氏體,溶入奧氏體中的鉬可大幅度提高淬透性,鉬和銅聯合使用,提高淬透性作用更大。經驗表明,當Cr/C為5~8時,加入2. 5% Mo,可使100mm斷面完全淬硬。設計成分Cr/C>7加入大于2%的鉬,對于厚度為90~100mm的大錘頭也能淬硬。
3)鎳(Ni)含量
鎳溶入奧氏體中,可充分發揮提高淬透性的作用,加入0. 5%的鎳,即可顯著提高淬透性,但它降低馬氏體開始點(M。)的作用比鉬大。加入鎳量控制在0.6%~1.0%。
4)銅(Cu)含量
銅與鎳類似,可全部溶于奧氏體中,對提高淬透性有利,但沒有鎳效果大,且銅在奧氏體中溶解度有限,約2%,熱處理后仍保留有少量殘余奧氏體,對提高韌性有利,但使硬度降低。所以銅控制在0.8%~1. 0%。
5)錳(Mn)含量
錳是穩定奧氏體元素,使組織中存在大量殘余奧氏體,錳能改變鉬在碳化物和金屬基體中含量的分配比,錳和鉬聯合加入可有效地提高淬透性,但錳強烈降低Ms點,增加鑄件開裂的趨向,對熔煉、鑄造、熱處理的微量變化敏感,所以含量不宜多,控制在0.8%~1.0%。
6)硅(Si)含量
硅是促進石墨化元素,固溶于基體中增加鑄鐵的脆性,硅降低淬透性,為了脫氧最少不得小于0. 3%,但硅提高慨點,我們控制硅在0. 4%~0.8%。
7)磷(P)、硫(S)含量
磷、硫均為有害元素,應盡量低,采用堿性爐熔煉,磷、硫可控制在0. 035%以下。
8)復合變質劑
為了凈化晶界,變質夾雜,細化晶粒,特別是為了使共晶碳化物變為條塊狀,在高硬度前提下獲得高韌性,我們采用了復合變質劑(Re +B、V、Ti等元素);對提高韌性起到了重要作用。
綜上所述化學成分設計范圍如表1。
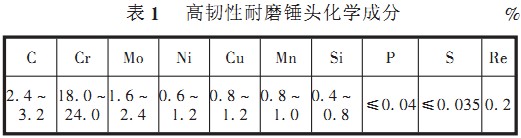
實際成分根據錘頭大小和工況條件做相應調整。按經驗公式,碳化物含量可達28%~30%。
2.2 熔煉工藝
采用300kg堿性爐襯中頻感應爐熔煉,先加入總配料量2/3的高碳鉻鐵及鉬鐵和廢鋼,熔化后分析碳鉻量,補加適量的高碳鉻鐵等合金元素,為節約成本,鎳常以不銹鋼邊腳料加入(配料時計入帶進的鉻)。
實際生產時,碳量低,則用廢電極增碳(收得率為50%左右),碳超標,則配適量的中、低碳鉻鐵。為控制磷、硫含量原則上不用生鐵增碳。
出鋼前10min加錳鐵,出鋼前7min加硅鐵進行沉淀預脫氧,出鋼前2min,采用深插鋁的方法進行擴散脫氧。當脫氧去氣充分鋼水花紋開始結疤,溫度在1450℃時出鋼。
3 裝機使用效果
自1997年課題成立以來,我們在實驗室試驗的基礎上,在院耐磨耐熱材料廠生產各種類型錘頭,重量從1.8~ 58kg/只,配套破碎機的臺時產量從10~200t/h,以破碎水泥熟料為主,并適用于石灰石、瓷石(白水泥原料)、硅石、煤矸石等。
錘頭的部分使用情況見表2。
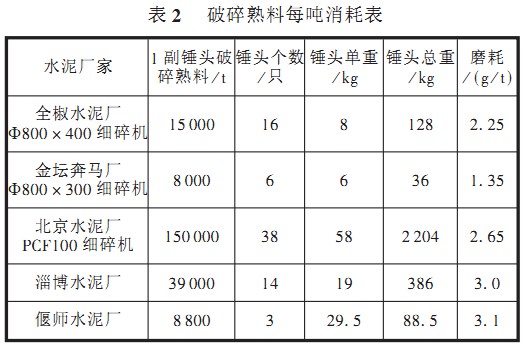
雖然這種錘頭售價較高,但由于它使用壽命是高錳鋼的5~6倍,使用費用仍只有高錳鋼的1/2,每年僅錘頭費用對于10萬t級水泥廠,即可節約3萬多元,況且節約5~6次維修時間,減少停機次數,確保了磨外預粉磨技術的充分發揮,使粉磨系統長期穩定增產、節能,對水泥廠的效益十分明顯。
三門峽富通新新能源銷售破碎機、顎式破碎機、圓錐式破碎機等。